Задние ведущие мосты "МАДАРА" АД
5.1 ЗАДНИЕ ВЕДУЩИЕ МОСТЫ
Эта инструкция по эксплуатации и уходу относится к задним ведущим мостам «МАДАРА» - тип 397.1 и 397.2, предназначеным для автобусов.
Прежде, чем приступить к эксплуатации транспортных средств, в которых установлены мосты, обслуживающему персоналу надо ознакомиться с содержанием настоящей инструкции.
Квалифицированное и добросовестное выполнение предписанных требований, соблюдение указанных в инструкции условий обеспечивают продолжительность и безопасность работы моста.
Производитель не несет ответственность за ущерб, возникший из за невыполнения предписанных в инструкции требований, а также требований, которые не указаны конкретно, но считаются общеизвестными в практике монтажного персонала и водителям транспортных средств.
Производитель оставляет за собой право вносить изменения.
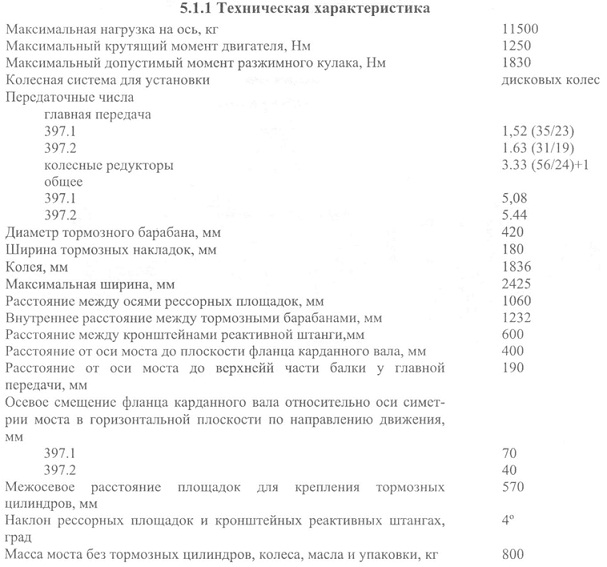
5.1.2 Техническая характеристика гипоидного моста
Максимальная нагрузка на мост, кг7000
Передаточное число 3,9; 4,22; 4,78; 5,37
Масса моста, кг 571
Тип тормозных камер "HALDEX" 20/24
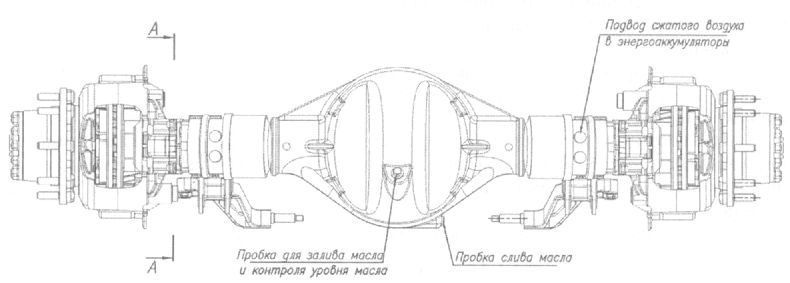
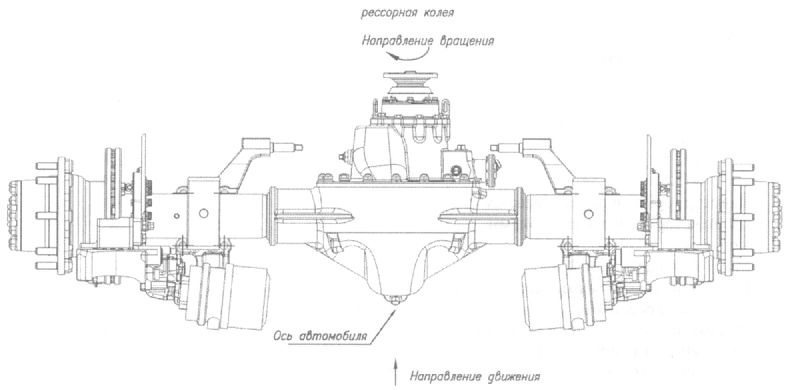

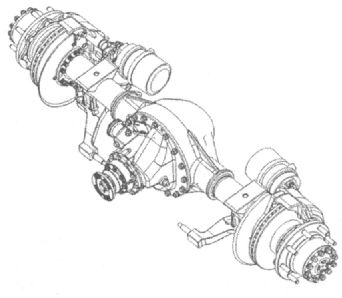
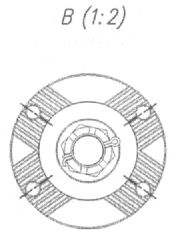
5.1.3 Конструкция
Задний мост - ведущий, двухступенчатый, имеет центральный конический редуктор и цилиндрические колесные (бортовые) передачи в ступицах задних колес.
Центральный редуктор - одноступенчатый, состоит из конических шестерен (главная передача) и межколесного конического дифференциала.
Ведущая шестерня главной передачи 5 (Рис. 464) посажена в стакане подшипников 6 на двух конических роликоподшипников 16 и 24. На шлицах ведущей шестерни установлен фланец карданного вала 15. Регулирование натяга конических роликоподшипников осуществляется с помощью регулировочных прокладок 19 ... 23, а регулировка зацепления зубьев конической пары - с помощью регулировочных прокладок 25...28. Установка конических подшипников в стакане позволяет осуществить регулировку самих подшипников с предварительным натягом, а затем регулировку зацепления за счет перемещения стакана с подшипниками. Коническая пара шестерен главной передачи при заводской сборке проходит предварительный подбор (спаривание). В случае необходимости замены одной из них менять нужно обе шестерни комплектно.
Дифференциальный механизм в главной передаче выполнен в виде конических шестерен. Две конические шестерни полуосей 40 и 51 (Рис. 465) разположены в чашки дифференциала 34 и 39, а четыре сателлита 38 находятся на двух взаимно перпендикулярных осях 50 дифференциала. Конические шестерни полуосей невзаимозаменяемы, так как в правой шестерни 40 предусмотрены отверстия, в которой входят штифты муфты блокировки дифференциала 61. Блокировка управляется пневматическим цилиндром с возвратной пружиной. Отверстия под оси дифференциала обрабатываются при собранном комплекте чашек. Поэтому чашки могут меняться только комплектом. В отверстия сателлитов запрессованы вложки 36, выполненные свертными из ленты. На левой чашке дифференциала смонтирована ведомая шестерня главной передачи 35. Дифференциал в сборе устанавливается в картере главной передачи 32 на конических подшипниках 44 закрепленных опорными кольцами (гайками) 31, служащими для регулировки подшипников и зацепления конической пары.
Гайки стопорятся пластинами 55. Картер главной передачи устанавливается в балке 29. Балка - стальная отливка с площадками для рессор и кронштейны реактивной штанги. Для предотвращения повышения давления в результате нагрева масла в балке имеется сапун.
Полуоси левая 30 и правая 49 - полностью разгруженного типа. Правая полуось длиннее левой.
Колесный редуктор (Рис. 466) заднего моста планетарного типа и устанавливается в ступицах задних колес в картере колесного редуктора. Ступицы колес 105 - стальные отливки, соединенные с картером колесных редукторов винтом 102. К этому узлу с помощью болта 103 закрепляется держатель сателлитных колес (водило) 118.
В держателях сателлитных колес118 запрессованы оси сателлитов, на которых на игольчатых роликах 113 поставлены сателлиты 114. На одну ось сателлита устанавливаются подшипники имеющие одинаковый класс допусков. На полуоси установлены ведущие шестерни колесного редуктора 121. Опорное колесо редуктора 111 свободно установлено на соединителе 108, который поставлен на шлицы цапфы 147 и закрепляется гайкой с прорезями 109.

Рис. 464 Ведущая шестерня главной передачи
1 - шайба пружинная; 2 - болт; 4 - втулка распорная; 5 - шестерня коническая ведущая; 6 - стакан подшипников; 7- кольцо; 8 - винт; 9 - прокладка; 10 - шайба пружинная; 11 - болт; 12 - крышка уплотнителя; 13 - манжета; 14 - гайка; 15 - фланец; 16 - подшипник; 18 - шплинт; 19....23 - прокладки регулировочные; 24-подшипник; 25...28 - прокладки регулировочные
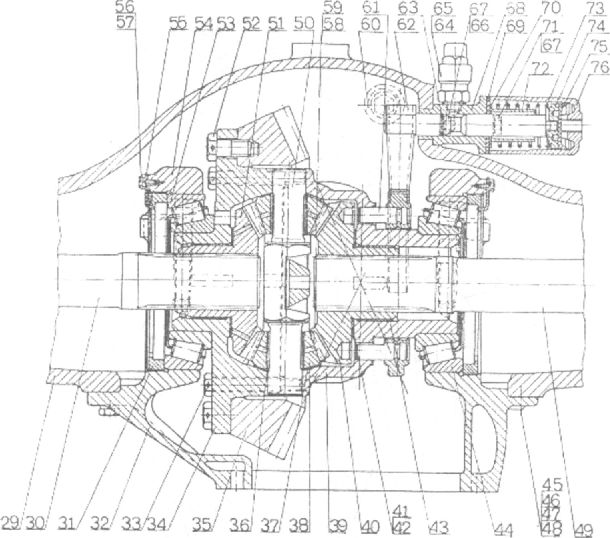
Рис. 465 Дифференциал
29 - балка; 30 - полуось левая; 31 - кольцо опорное; 32 - картер главной передачи; 33 - болт; 34 - чашка дифференциала левая; 35 -- шестерня коническая ведомая; 36 - вложка сателлитов; 37 - шайба опорная сателлитов; 38 - сателлит дифференциала; 39 - чашка дифференциала правая; 40 - шестерня полуоси правая; 41 и 42 - шайба опорная; 43 - вложка шестерни полуоси; 44 - подшипник; 45 - болт; 46 - шайба пружинная; 47 - болт; 48 - шайба пружинная; 49 - полуось правая; 50 - ось сателлитов; 51 - шестерня полуоси левая; 52 - болт; 53 - болт; 54 - крышка;55 - пластина стопорная; 56 - болт; 57 - шайба пружинная; 58 - пробка магнитная; 59 - кольцо; 60 - пробка; 61 - муфта блокировки дифференциала; 62 - вилка блокировка дифференциала; 63 - «о» - кольцо; 64 - кнопочный выключатель;65 - кольцо; 66 - гайка; 67 - шайба пружинная; 68 - надставка цилиндра блокировки; 69 - уплотнитель; 70 - шайба;71 - болт; 72 - втулка; 73 - пружина; 74 - поршень; 75 - манжета; 76 - цилиндр блокировки дифференциала
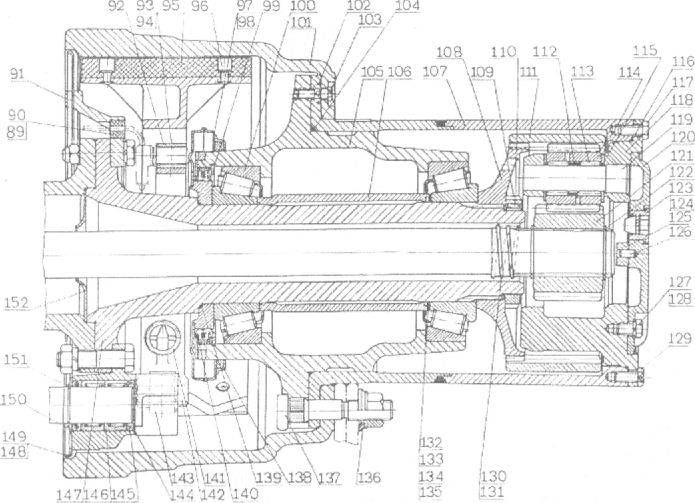
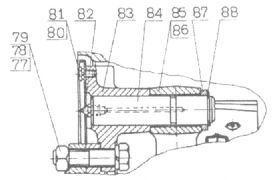
Рис. 466 Тормозной механизм и колесный редуктор
77 - болт; 78 - гайка; 79 - шайба; пружинная; 80 - болт; 81 - шайба пружинная ; 82 - пресс - масленка; 83 -носач; 84 - палец тормозных колодок; 85 - колодка верхняя; 86 - колодка нижняя; 87 - планка соединительная; 88 - кольцо стопорное; 89 - втулка резиновая; 90 - втулка резиновая; 91 - скоба; 92 - датчик АБС; 93 - болт; 94 - шайба пружинная ; 95 - накладка; 96 - заклепка; 97 - кольцо маслособирательное правое; 98 - кольцо маслособирательное левое; 99 - кольцо стопорное; 100 - подшипник; 101 - барабан; 102 - винт; 103 - болт; 104 - «о» - кольцо; 105 - ступица; 106 - втулка; 107 - картер колесного редуктора; 108 - соединитель; 109 - гайка с прорезями;110 - винт; 111 - колесо опорное; 112 - втулка распорная;113 - игла; 114 - сателлит; 115 - шайба опорная сателлитов; 116 - «о» - кольцо; 117 - болт; 118 -держатель сателлитных колес; 119 - ось сателлитов; 120 - крышка; 121 - ведущая шестерня; 122 - кольцо стопорное; 123 - пробка магнитная; 124 - кольцо; 125 - опора; 126 - щифт; 127 - болт; 128 - шайба пружинная; 129 - болт отмеченый;130 - спираль левая; 131 - спираль правая; 132...135 - прокладка регулировочная; 136 - гайка; 137 - болт барабанный; 138 - уплотнитель; 139 - «о» - кольцо; 140 - уплотнитель; 141 - пружина тормозных колодок; 142 - ось ролика; 143 - ролик для колодки; 144 - шайба; 145 -уплотнитель; 146 - ролик игольчатый; 147 - рукав; 148 - щит; 149 - заглушка; 150 - кольцо опорное; 151 -кольцо стопорное; 152 - шайба направляющая
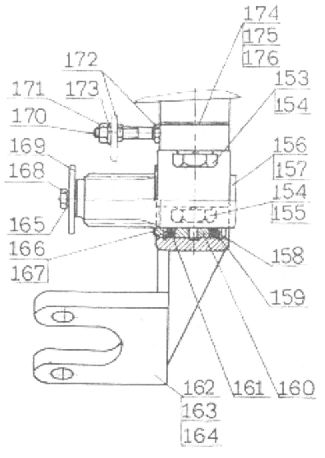
Рис. 467 Рычаги разжимных кулаков
153-болт; 154- шайба пружинная; 155- болт; 156- кулак разжимной левый; 157- кулак разжимной правый; 158 - кольцо стопорное; 159 - крышка; 160 - втулка; 161 - «о» - кольцо;162 - кронштейн тормозного цилиндра - левый; 163 - кронштейн тормозного цилиндра - правый; 164 - пресс - масленка; 165 - шайба пружинная; 166 и 167 - уплотнитель; 168 - болт; 169 - прокладка; 170 - шпилька; 171 - гайка; 172-гайка; 173- шайба; 174...176 - шайба быстросъемная
Колесный редуктор закрывается крышкой 120, на которой имеется маслозаливное отверстие, закрываемое пробкой 123 и отверстие для слива масла из колесного редуктора, закрываемое отмеченым болтом 129. В крышку запрессован щифт 126, на который ставится опора 125, с помощью которой регулируется аксиальный зазор полуоси.
Тормоз барабанного типа, с двумя внутренними литыми колодками 85 и 86 расположенными на отдельных пальцах 84. Тормозной механизм включает суппорты 83, которые крепятся болтами 77 к балке. Тормозные накладки 95 к колодкам тормоза крепятся заклепками 96. Тормозной механизм защищен от попадания масла из ступицы колес (при возможном повреждении манжеты 140) маслособирательным кольцом 97, 98 со сливной трубкой. Против грязи механизм закрыт щитом 148.
На шлицевом конце разжимных кулаков 156 и 157 (Рис. 467) устанавливаются автоматические регулировочные рычаги, соединенные с тормозной камерой.
Разжимные кулаки установлены в суппортах колесных тормозов на игольчатых подшипниках 113 (Рис. 466) и в кронштейных тормозных камер 162 и 163 (Рис. 467) на втулках 160.
5.1.4 Описание механизмов
БАЛКА: стальная отливка с площадками для рессор и кронштейнов реактивной штанги. К фланцу балки болтами крепится картер, главной передачи и рукава, на которых устанавливаются ступицы колес. На специальных площадках крепятся кронштейны тормозных камер.
ГЛАВНАЯ ПЕРЕДАЧА: состоит из картера, в котором на двух конических подшипниках вращаются чашки дифференциала с конической короной шестерней. К картеру прикреплен стакан подшипников, в котором на двух конических подшипниках установлена ведущая шестерня главной передачи. Коническая пара главной передачи имеет зуба типа "СПИРОМАТИК" фирмы "ОЕРЛИКОН" Швейцария. На шлицах шестерни установлен фланец карданного вала.
ДИФФЕРЕНЦИАЛ: конический, с четырьмя сателлитами, установленными на двух взаимно перпендикулярных осях. Предусмотрена блокировка, которая управляется пневматическим цилиндром с возвратной пружиной. Включение блокировки сигнализируется электрическим контактным датчиком.
СТУПИЦЫ КОЛЕС: стальные отливки, соединенные с картером колесных редукторов винтами. Вращаются на двух конических подшипниках установленных на рукавах.
ТОРМОЗНОЙ МЕХАНИЗМ: включает суппорты, которые крепятся болтами к балке, на которых смонтированы литые тормозные колодки. Разведение тормозных колодок осуществляется разжимными кулаками с эволвентным профилем, действующими на ролики , установленных на осях колодок. Разжимные кулаки приводятся в движение тормозными рычагами, с прямобочными шлицами. В тормозных рычагах находится червячный механизм, позволяющий регулировать тормозной зазор. Возврат тормозных колодок осуществляется пружинами. Тормозные барабаны изготовлены из серого чугуна с предписанным химическим составом и крепяться болтами к ступицам и картерам колесных редукторов.
КОЛЕСНЫЕ РЕДУКТОРЫ: планетарного типа, каждый имеет по 5 сателлитов, со свободно установленной короной шестерней с внутренними зубьями и центральной шестерней на полуоси, плавающей свободно. Каждый сателлит установлен на двух рядах игольчатых роликов одного класса точности. Оси сателлитов запресованы в держателе сателлитов, который передает вращающий момент ступице посредством болтов.
5.1.5 Техническое обслуживание
Надежность в процессе эксплуатации и длительный срок службы обеспечиваются регулярным выполнением работ по техническому обслуживанию, которые включают следующие операции:
Ежедневное ТО.
1.Наружным осмотром проверить состояние гаек колес и герметичность моста.
2.Проверить эффективность тормозного механизма посредством пробного торможения.
ТО на каждые 7500 км пробега.
1.Подтянуть гайки колес.
2.Почистить сапун.
3.Проверить уровень масла в картере главной передачи и колесных редукторах и если необходимо, долить. Первоначальная проверка производится после 2000 км пробега, а первая смена масла после 7500 км пробега.
4.Смазать подшипники разжимных кулаков, оси тормозных колодок и червячного механизма тормозных рычагов.
5.Почистить концы и проверить проходимость масла из маслоудаляющих трубок.
6.Проверить зазор между тормозной накладкой и рабочей поверхностью тормозного барабана.
7.Проверить и при необходимости подтянуть внешние крепежные элементы.
ТО на каждые 30000 км пробега.
-Проверить зазор между тормозными барабанами и накладками колодок.
-Сменить масла.
Указания по смазке. Периодичность смазки маслом и консистентными смазками и необходимые количества указаны в Таблица 71
Таблица 71 Периодичность смазывания
Место смазки | Количество, л | Выполняемая оперяция | |
Проверка уровня | Смена масла | ||
Картер главной передачи | 7,5 | Через каждые 7500 км пробега | Первая смена после 7500 км пробега. Следующие черезкаждые 30000 км пробега |
Колесные редукторы | 2,5+2,5 | ||
Стакан подшипников шестерни | 0,250 | Только при первоначальномпрокручивании | |
Подшипники разжимных кулаков. Оси тормозных колодок.Червячный механизм тормозных рычагов | До необходимого количества | Через каждые 7500 км пробега |
Если в продолжении одного года мост имел пробег меньше, чем 30000 км, смену масла надо осуществить в рамках одногодичного периода.
Рекомендуемые смазочные материалы приведены в Таблица 72.
Таблица 72 Рекомендуемые смазочные материалы
Трансмиссионные масла | Консистентные смазки |
ТМ-5/90БДС14368- 82 ТАп -15В ГОСТ 23652 - 79 ТСп -15К ГОСТ 23652-79 OAРР90 CSN Или другие с качеством по API -GL - 5 и вискозитетномклассе по SAE 90 | АФС 3 об В1/Н001 - HI 11/РС01 БДС 1415 -84 Литол24ГОСТ 21150-75 AV-2 или NH-2 CSN Замечание. 1 .Не допускается смешивание различных сортов маселввиду различных присадок в их составе. 2. Рекомендуемые масла и консистентные смазкипригодные, когда задние мосты эксплуатируются в нормальных дорожныхусловиях и в умеренном климатичном поясе. |
Места смазки и пресс - масленки указаны на Рис. 470, Рис. 468 и Рис. 469
1.Картер главной передачи (балка).
поз. 1 - маслозаливная и контольная пробка.
поз. 2 - сливная пробка.
поз. 3 - маслозаливная пробка в стакане подшипников конической шестерни.
2.Колесные редукторы.
поз. 4 - маслозаливная и контрольная пробка.
поз. 5 - сливная пробка (отмеченый болт).
3.Места для смазки с конссистентными смазками.
поз. 6 - пресс - масленки червячных механизмов тормозных рычагов.
поз. 7 - пресс - масленки втулок разжимных кулаков в кронштейнах тормозных камер.
поз. 8 - пресс - масленки втулок разжимных кулаков в суппортах тормозных колодок.
поз. 9 - пресс - масленки осей тормозных колодок 5.3.4.
4. Другие.
поз. 10 - сапун
поз. 11 - масловыпускательные трубки
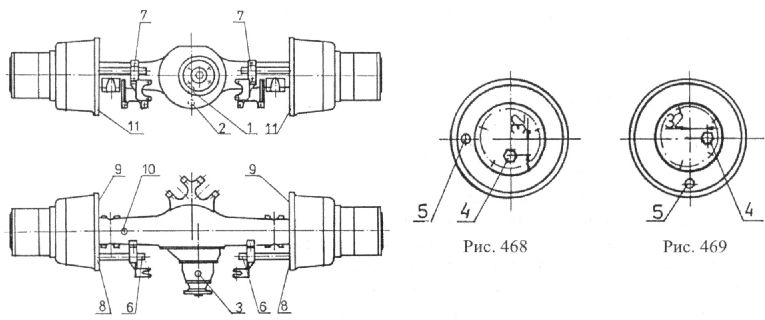
Рис. 470
ОПЕРАЦИИ ПО ТЕХНИЧЕСКОМУ ОБСЛУЖИВАНИЮ
1. Проверка уровня масла
1.1.Транспортное средство устанавливается на горизонтальной, равной площадке. Для обеспечения этой операции мост можно поднять на стабильную опору, а передние колеса застопорить с двух сторон упорами.
1.2.Проверка уровня масла всегда начинается с колесных редукторов. Колесо поворачевается таким образом, что бы контрольная пробка поз. 4 (Рис. 468) достигла самого низкого положения. Тогда уровень масла должен доходить до нижней кромки отверстия. Если нужно, можно долить масло, используя то же отверстие.
1.3.Проверку уровня масло в картере главной передачи можно осуществить через пробку поз. 1 (Рис. 470), Уровень масла должен доходить до нижней кромки отверстия. Если нужно, можно долить масло используя то же отверстие.
1.4.Если надо долить масло, не допускается смешивание разных сортов масел.
2. Смена масла
2.1.Отработанное масло в сроках указанных в Таблица 71, заменяется после предварительной подготовки в соответствий с п. 1.1. Колеса поворачиваются так, что отмеченые болты колесных редукторов поз. 5 (Рис. 469) заняли бы самое низкое положение, как указано на Рис. 470. Под отверстия колесных редукторов надо положить лист, что бы масло не стекало по шинам. Слив масла надо осущуствлять при его рабочей температуре.
2.2.Вывертываются отмеченые болты поз. 5 (Рис. 469) колесных редукторов и поз. 2 (Рис. 470) под картер главной передачи (балки).
2.3.Очистить магнитные вставки пробок, а потом ввернуть их. Колеса надо повернуть таким образом, что бы пробки поз. 4 (Рис. 468) заняли самое низкое положение.
2.4.Налить необходимое количество масла через пробки поз. 4 (Рис. 468) колесных редукторов. Уровень масла должен доходить до нижней кромки отверстия, когда отверствие контрольной пробки находится в самом низком положении. Операция осуществляется для обеих колесных редукторов. Залить масло в картер главной передачи до нижней кромки отверстия пробки поз. 1 (Рис. 470).
2.5.Надежно закрутить пробки и проверить не наблюдается ли подтекание масла.
2.6.Во время смены масла и при первоначальном пуске транспортого средства в движение (в том числе после ремонта) надо залить 0,250л. масла через пробки в крышке подшипников главной передачи поз.З (Рис. 470). Таким образом осуществляется правильное смазывание подшипников конической шестерни, прежде чем начнется подача масла к ним от короны главной передачи.
3.Смазывание консистентной смазкой
3.1.Смазывание консистентной смазкой осуществляется солидолонагнетателем, ручным или машинным способом в соответствии с указаниями в Таблица 71 на следующих местах:
-червячные механизмы тормозных рычагов поз. 6 (Рис. 470)
-подшипники разжимных кулаков поз. 7 и 8 (Рис. 470)
-оси тормозных колодок поз. 9 (Рис. 470)
3.2.Во время смазывания консистентной смазкой осей тормозных колодок, нужно нагнетить столько смазки, сколько необходимо, чтобы она не достигла рабочих эллементов тормоза. Ориентировочное количество приблизительно 3 куб. см.
4.Очистка сапуна и масловыпускающих трубок.
4.1.Сапун надо всегда поддерживать чистым, так как в противном случае в картере создается сверхдавление и возможна утечка масла через манжетные уплотнители. Сапун разположен на верхней части балки моста поз. 10 (Рис. 470).
4.2.Масловыпускательные трубки выходят из внутреннего края супортов поз. 11 (Рис. 470) и используются для отвода масла в случае пропуска манжетного уплотнителя ступицы. Во время проверки надо установить их исправность, почистить наконечники, а также проверить их проводимость. Если установлена утечка масла, надо осуществить демонтаж и сменить уплотнители Stefa system 500 1HHI 155x190x17.54+HR (NBR).
5.Затяжка резьбовых соединении
5.1.Подтягивание внешних резьбовых соединений осуществить крутящим моментом согласно Таблица 73. Особое внимание надо обратить своевременному креплению гаек на колесах.
5.2.При первоначальной установки нового заднего моста первая подтяжка рекомендуется после 100 км пробега, а вторая после 500 км пробега.
Таблица 73 Моменты затяжки резьбовых соединении
Соединяемые детали | Размер резьбы | Материал | Количесво, шт. | Момент затяжки Нм |
1 .Картер главной передачи - балка | М12 | 8.8 | 12 | 7,5 |
2.Рукав- балка | М18х1,5 | 8 | 24 | 25,0 |
3.Кронштейн тормозных камер - балка | М16х 1,5 | 8.8 | 4 | 16,0 |
4.Рычаг - разжимной кулак | М8 | 8.8 | 2 | 2,0 |
5.Гайка для барабанного болта | М22х1,5 | 10.0 | 20 | 60,0 |
6.Соединитель -рукав | М90х2 | 5 | 2 | 50,0 |
7.Картер главной передачи - крышкаподшипников | М16Х1,5 | 8.8 | 4 | 16,0 |
8.Чашки дифференциала правая -левая | М12х1,5 | 10.9 | 12 | 10,0 |
9.Шестерня ведомая - чашка дифференциала | М16х1,5 | 10.9 | 12 | 22,0 |
10.Стакан подшипников - картер гл.передачи | М14 | 8.8 | 8 | 12,0 |
11 .Крышка уплотнителя - стаканподшипников | М8 | 8.8 | 8 | 2,0 |
12.Фланец - шестерня конической передачи | М42х1,5 | 10 | 1 | 50,0 |
13.Держатель сателлитов - крышка | М12х1,5 | 8.8 | 10 | 7,5 |
14.Суппорт колесных тормозов -предохранительныйщит | М8 | 8.8 | 12 | 2,0 |
15. Держатель сателлитов - картер колесногоредуктора | М12х1,5 | 10.9 | 40 | 10,0 |
ПРИМЕЧАНИЕ: Отклонение затяжных моментов +/-5%. |
5.1.6 Ремонт
Настоящая инструкция по ремонту предназначена для ремонтных предприятий и содержит описание, основные технические и регулировочные данные и предписания, знание которых позволяет выполнить качественный ремонт и правильную регулировку задних ведущих мостов «МАДАРА» типа 397.1 и 397.2.
Прежде, чем приступить к ремонту задних мостов необходимо, чтобы персонал по ремонту хорошо ознакомился с содержанием настоящей инструкции.
Для выполнения ремонтных работ рекомендуется пользоваться специальным инструментом и оснасткой, которые указаны в тексте и в Таблица 74.
Для замены узлов и деталей пользуйтесь только оригинальными узлами, деталями, выпускаемыми фирмой «МАДАРА».
Смазывать детали в процессе сборки, а также заправлять мосты после проведения ремонта разрешается только трансмиссионными маслами и консистентными смазками, указанными в инструкции.
Резьбовые соединения затягивать динамометрическим ключом. Рекомендуемые моменты затяжки приведены в Таблица 75.
Завод - изготовитель не несет ответственность за ущербы, возникшие из за невыполнения предписанных в инструкций требовании, а также несоблюдения требованиях и правил, не указанных в настоящей инструкции, но считающихся обязательными и общепринятыми в практике ремонтного персонала, в том числе и правил техники безопасности.
Завод - изготовитель оставляет за собой право на внесение изменений.
Таблица 74 Ремонтные инструменты для демонтажа и монтажа заднего моста
Наименование | Обозначение | |
для демонтажа | для монтажа | |
Стойка для сборки картера главнойпередачи | Т 17-377 | Т 17-377 |
Приспособление для снятия ступицы колес и картераколесного редуктора | Т 17-2256 | |
Приспособление для монтажа ступицы колес нацапфы | Т17- 1567 | |
Ключ для опорного кольца подшипниковдифференциала | Т 17-393 | Т 17-393 |
Ключ для гаек с прорезями рукава | Т 17-402 | Т 17-402 |
Рычаг для установки пружин тормозныхколодок | Т 17-411 | Т 17-411 |
Дорн для установки подшипника разжимного кулака всуппорт тормозных колодок | Т 17-1453 | |
Дорн для установки подшипника разжимногокулака | Т 17-1457 | |
Дорн для замера аксиального зазора шестерендифференциала | Т 19-1039 | |
Приспособление для заклепки тормозных накладок напрессе | Т51 - 1102 | |
Ключ 10,13 | Т 19-1110 | Т 19-1110 |
Ключ 17,22 | Т 19 - 1033 | Т 19-1033 |
Ключ 19 | Т 19-1040 | Т 19-1040 |
Ключ 24 | Т 19-1034 | Т 19-1034 |
Рычаг для ключа | Т 19-1037 | Т 19-1037 |
Таблица 75 Моменты затяжки резьбовых соединений
Соединяемые детали | Размер резьбы | Материал | Количество, шт | Момент затяжки, Н*м |
Картер главной передачи -балка | М12 | 8.8 | 12 | 7,5 |
Цапфа- балка | М18х1,5 | 8 | 24 | 25,0 |
Кронштейн тормозных камер -балка | Ml 6x1,5 | 8.8 | 8 | 16,0 |
Рычаг - разжимной кулак | М8 | 8.8 | 2 | 2,0 |
Гайка для барабанного болта | М22х1,5 | 10.0 | 20 | 60,0 |
Соединитель -цапфа | М90х2 | 5 | 2 | 50,0 |
Картер главной передачи - крышкаподшипников | М16Х1,5 | 8.8 | 4 | 16,0 |
Чашки дифференциала правая -левая | М12х1,5 | 10.9 | 12 | 10,0 |
Шестерня ведомая - чашкадифференциала | М16х1,5 | 10.9 | 12 | 22,0 |
Стакан подшипников - картер гл. передачи | М14 | 8.8 | 8 | 12,0 |
Крышка уплотнителя - стакан подшипников | М8 | 8.8 | 8 | 2,0 |
Фланец - шестерня конической передачи | М42х1,5 | 10 | 1 | 50,0 |
Держатель сателлитов - крышка | М12х1,5 | 8.8 | 10 | 7,5 |
Суппорт колесных тормозов - предохранительныйщит | М8 | 8.8 | 12 | 2,0 |
Держатель сателлитов - картер колесногоредуктора | М 12x1,5 | 10.9 | 40 | 10,0 |
ПРИМЕЧАНИЕ: Отклонение затяжных моментов +/ -5%. |
На каждый задний мост ставится табличка или выбивается производственный номер: Примерное обозначение (состав производственного номера) следующее:
3 1 А 397.1; 0012
3 - год производства2003 год
1 - месяц производства январь
А - фирма изготовитель "МАДАРА" Шумен
397.1 - тип моста (индекс чертежного номера)
0012 - порядковый номер моста с начала месяца
5.1.6.1 Регулировочные данные
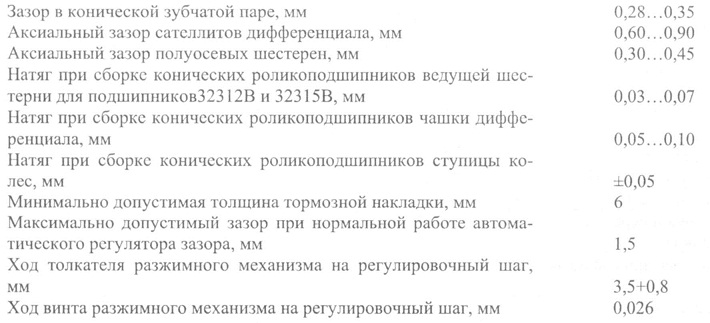
5.1.6.2 Снятие заднего моста с автобуса
-Установить автобус на осмотровую канаву.
-Ослабить затяжку гаек крепления колес.
-Выпустить масло через сливные отверстия заднего моста (Рис. 491). При этом колеса надо установить в такое положение, чтобы болты сливных отверстий находились внизу. Под отверстия надо положит изогнутые пластины, для предотвращения попадания масла на шины.
-Отсоединить шланги подвода воздуха к тормозным камерам.
-Поднять заднюю часть автобуса и опустить на подставку.
-Снять карданный вал и колеса. При снятии карданного вала предотвратить проворачивание балки моста так, чтобы его передний край не ударился о пол площадки. Под задний мост подкатить монтажную тележку, отвернуть гайки рессорных стремянок и снять мост с задних рессор.
-Выкатить тележку с мостом из под автобуса.
5.1.6.3 Разборка заднего моста
-Снятый с автобуса задний мост рекомендуется поставить на монтажную тележку и разбирать на ней.
-Отвернуть тормозные камеры и снять их.
-Разобрать держатель сателлитных колес 118 (Рис. 466) , колпачок держателя сателлитных зубчатых колес 120, штифт 126, опору 125, стопорное кольцо 122 и снять держатель сателлитных зубчатых колес вместе с последними, вытащить ведущую шестерню 121 колесного редуктора.
-Ведущие шестерни колесных редукторов можно снять вместе с полуосями 30 и 49 (Рис. 465).
-Отвернуть фиксирующий винт110 (Рис. 466) и с помощью ключа Т17- 402 отвернуть гайку с прорезями 109 (Рис. 466). Ступицу колеса вместе с картером колесного редуктора, снять с помощью приспособления Т17- 2256 (Рис. 471).
-Со ступицы колеса снять уплотнитель 140 (Рис. 466) и при необходимости выбить наружные кольца конических роликоподшипников 100. При обратной сборке не допускается перестановка мест колец.
-Пружины тормозных колодок 141 снять с помощью приспособления (рычага) монтажа последних Т17-411, снять стопорные кольца 88 и соединительную планку 87. Освобожденные тормозные колодки вынуть из держателя колодок. С внутренней стороны освободить щит 148. Тормозные колодки можно снять и без снятия ступицы колеса.
-Разжимные кулаки 156 и 157 (Рис. 467) не разбираются.
-В зависимости от необходимости, отвернуть гайки 78 (Рис. 466), после чего снять, рукав 147 вместе с направляющей шайбой 152 (правая и левая сторона).
-После отворачивания болтов 2 (Рис. 464) снять с балки моста 29 (Рис. 465) картер главной передачи 32, вместе со стаканом подшипников 6 (Рис. 464). Картер можно освободить с помощью специальных болтов 47 (Рис. 465) показанных стрелкой на Рис. 472. Освобожденный картер поставить на стойку для сборки картера главной передачи Т17-377.
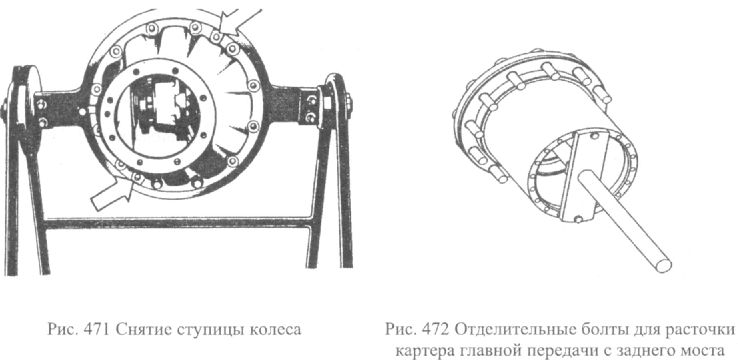
-В зависимости от необходимости разобрать картер главной передачи, чашки дифференциала и стакан подшипников. Для опорного кольца подшипников 31 (Рис. 465) использовать ключ Т17-393 (Рис. 473).При разборке чашки дифференциала следует подходящим способом пометить взаимное расположение осей сателлитных зубчатых колес во избежание их перестановки. При разборке крышек подшипников тоже не допускается их перестановка.
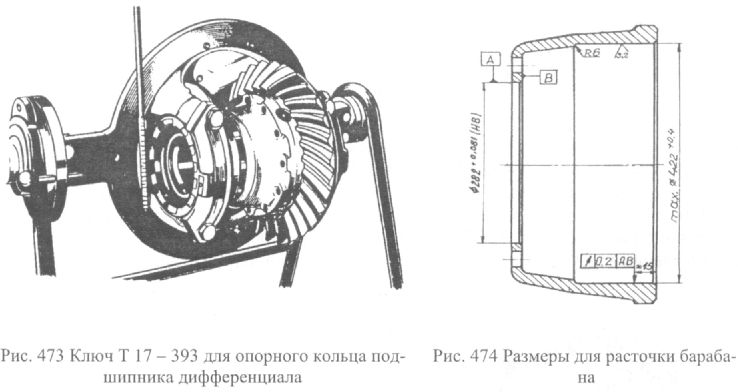
-При разборке и сборке заднего моста надо использовать специальные ключи, которые указаны в Таблица 74.
Контроль технического состояния.
Внешним осмотром проверить состояние корпусных деталей мостов.
Не допускается эксплуатация с такими дефектами, как: трещины на балке и рукавах, износ и срыв резбы в отверстиях под пробки и болты. На шестернях главной передачи, дифференциала и колесных редукторов не допускается наличие трещин и сколов в средней части зуба, питтинга на площади более 25% поверхности зуба.
Шестерни, имеющие сколы вершин зубьев на длине не более 5 мм от торца зуба, после зачистки сколов допускаются для дальнейшей работы.
Подшипники имеющие сколы, трещины, разрушение сепараторов, а также выкрашивание, раковины, глубокие риски и бринеллирование на беговых дорожках колец и роликах, забраковать.
Уплотнительные манжеты и «О» - кольца заменить при разрывах, износе, затвердевании и растрескивании рабочих кромок.
Если глубина утопания головок заклепок крепления тормозных накладок менее 0,5 мм, то накладки следует заменить новыми.
5.1.6.4 Сборка заднего моста
Общие требования к сборке.
Все детали должны быть чистыми и без повреждений. Особое внимание следует обратить, чтобы болты и гайки были с предписанными механическими качествами.
При замене деталей новыми следует всегда руководствоваться каталогом запасных частей. Некоторые детали нельзя заменить в отдельности, а только в комплекте. Таковыми являются:
-пара конических шестерен (ведущая и ведомая), обкатанных вместе в комплекте;
-картер главной передачи с крышками подшипников дифференциала (отверстия для подшипников обрабатываются вместе, в собранном состоянии);
-правая и левая чашки дифференциала (отверстия осей сателлитных зубчатых колес обрабатываются вместе, в собранном состоянии);
-пара тормозных колодок;
-маслособирательное кольцо.
При сборке некоторых деталей, одинаковых по внешнему виду, может произойти их неправильная перестановка. Это касается прежде всего следующих деталей:
-левая и правая шестерня полуоси;
-левый и правый разжимной кулак;
-левый и правый рычаг разжимного кулака;
-нижняя и верхняя тормозная колодка;
-пробки заливного и сливного отверстия в балке моста
-сливная пробка с магнитом.
Замена тормозных накладок.
Тормозные колодки разбираются после снятие колеса и тормозного барабана. При снятии пружины тормозных колодок не допускать их повреждение. Снять тормозные колодки и заклепать новые накладки с помощью приспособления для заклепки на прессе. При сборке не допускать замены мест верхней и нижней тормозной колодки.
Если нужно расточить тормозные барабаны, изготовитель разрешает следующие размеры (Рис. 474):

Сборка и регулирование узлов и подгрупп.
Балку заднего моста 29 (Рис. 465) установить на тележку с колесами, причем отверстие, к которому присоединяется картер главной передачи, должно быть направлено вверх.
В стакан подшипников 6 (Рис. 464) напрессовать наружные кольца подшипников 16 и 24, ввести внутренние кольца и произвести замер. С целью получения правильных значений вычислений для всех деталей (особенно для подшипников) детали собирать несмазанными. От правильной сборки конических роликоподшипников зависит работа и долговечность остальных деталей, поэтому следует выполнять все требования и указания.
При сборке ведущей шестерни конической пары с коническими роликоподшипниками нужно сделать следующие расчеты:
Толщина регулировочных прокладок X, согласно Рис. 475 определяется следующим соотношением:
T = U +V + X + (0.05 + 0.10),
из которого для X получается:
X = T- U- V- ( 0.05 + 0.10 ), где
Т - расстояние между задними (по направлению движения) опорными поверхностями внутренних колец конических роликоподшипников;
U - ширина внутреннего кольца конического роликоподшипника;
V - ширина распорной втулки;
X - толщина регулирующих прокладок;
0.05, 0.10 - натяг конических роликоподшипников.
Для получения размера Т в стакане подшипников установить наружные кольца подшипников, вставить внутренние кольца подшипников и замерить размер Т (Рис. 476). По определенному из вычислений значению X подобрать прокладку соответствующей толщины.
Размеры регулирующих прокладок следующие:
производственный № прокладки толщина, мм
41 - 085 - 5101 0.2
41 - 086 - 5101 0.3
41 - 087 - 5101 0.5
41 - 088 - 5101 1.0
41 - 089 - 51011.5
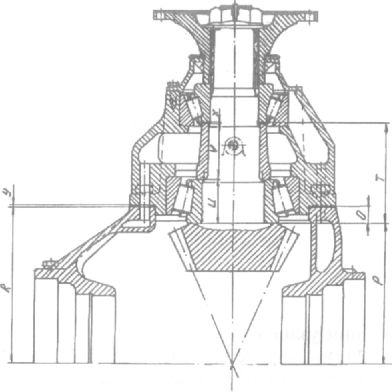
Рис. 475 Расчет толщины регулировочных прокладок главной передачи
Ориентировочные значения размеров Т, U и V следующие:
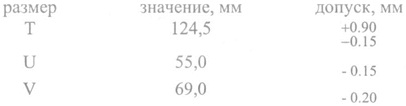
При сборке ведущей и ведомой шестерни конической пары нужно взаимное регулирование для достижения правильного зацепления. Для этого используются регулирующие прокладки, вставляемые между стаканом подшипников и картером главной передачи.
Толщина регулирующих прокладок, согласно Рис. 475 вычисляется по формуле:
0 + P = R + Y± 0,05
из которого для Y получается:
Y ± 0.05 = О + Р - R, где
О - расстояние между опорной поверхностью внутреннего кольца конического роликоподшипника и контактирующей поверхностью стакана подшипников (Рис. 477).
Р - расстояние между торцевой опорной поверхностью ведущей шестерни и осевой линией ведомой шестерни конической пары. Ее значение определяется при лапинговании пары конических зубчатых колес на лапинг машине. Действительное значение этого размера записано на торце ведущей шестерни. На торце ведущей шестерни записан также и порядковый номер сработанной (лепингованной) зубчатой пары.
R - расстояние между контактирующей поверхностью картера главной передачи к которой подводится стакан подшипников и осевой линией отверстия для подшипников дифференциала. Отклонение от номинального размера 190 выбито на картере главной передачи (Рис. 478) - обозначение А.
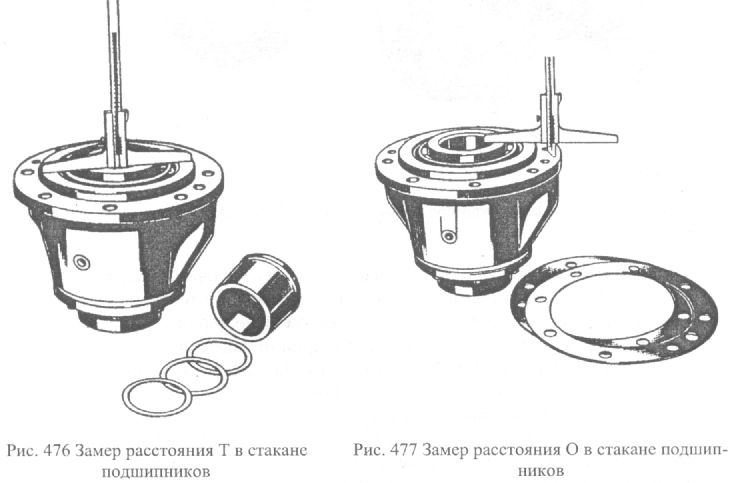
Размеры регулирующих прокладок следующие:
производственный № прокладки | толщина, мм | |
для 397.2 | ||
41 | - 100-5101 | 0.2 |
41 | - 101-5101 | 0.3 |
41 | - 102-5101 | 0.5 |
41 | - 103-5101 | 1.0 |
для 397.1 | ||
41 | -325-5101 | 0.2 |
41 | -324-5101 | 0.3 |
41 | -322-5101 | 0.5 |
41 | -323-5101 | 1.0 |
Номинальные значения размеров О, Р и R следующие:

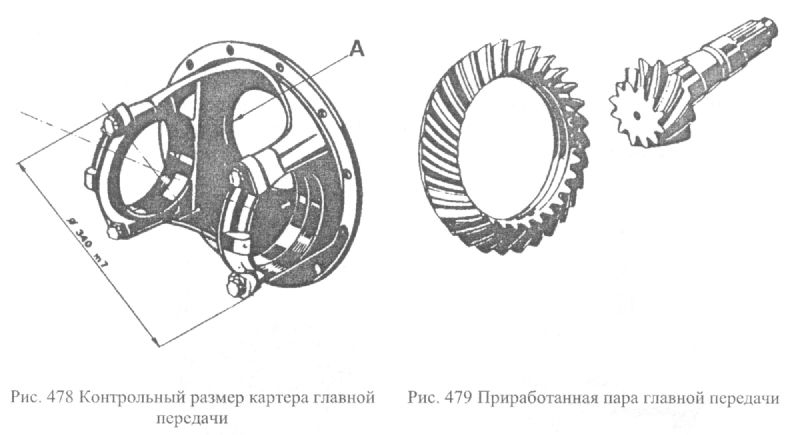
Па Рис. 479 показана приработанная пара конических зубчатых колес.
На Рис. 480 показаны примеры взаимного зацепления зубьев в конической паре с помощью нанесенных контактных пятен на зубьях ведомой шестерни.
Известно, что при смещении ведомой шестерни от зацепления появляется зазор, значение R которого составляет от 50 до 75 % от расстояния смещения, в то время, как при смещении ведущей шестерни изменения в зацеплении относительно невелики. При правильном зацеплении зубьев значение бокового зазора должно находиться в интервале 0.28.. .0.35 мм.
Примеры контактных пятен на зубьях ведомой шестерни при зацеплении конических зубчатых колес (Рис. 480) относятся к следующему:
А - правильное зацепление при полной нагрузке.
Б - правильное зацепление при частичной нагрузке или без нагрузки. Контактное пятно занимает 35...50 % длины зуба и 50...80 % высоты эвольвентного профиля зуба.
В - внутреннее зацепление с коротким пятном. В этом случае ведущая шестерня смещена во внутрь, а ведомая - наружу от зацепления.
Г - внешнее зацепление, которое не происходит, если зазор в зубчатой паре правильно отрегулирован. Этот тип зацепления приводит к шумному ходу конической пары и к перелому зубьев. Для достижения правильного зацепления необходимо ведомую шестерню сдвинут вовнутрь, а ведущую - наружу от зацепления.
Д - поперечное зацепление с контактным пятном у кромки зуба при движении вперед и на наружной стороне при движении назад.
Такой вид зацепления приемлем, если пятно занимает 5/8 длины зуба. Обратное зацепление (на наружной стороне при движении вперед и у кромки зуба при движении назад) недопустимо.
Е - коренное зацепление с контактным пятном у самого корня зуба. В этом случае ведомая шестерня смещается вовнутрь, а ведущая- наружу от зацепления.
Ж - кромковое зацепление с контактным пятном у самой головки зуба. В этом случае ведущая шестерня перемещается вовнутрь а ведомая - наружу от зацепления.
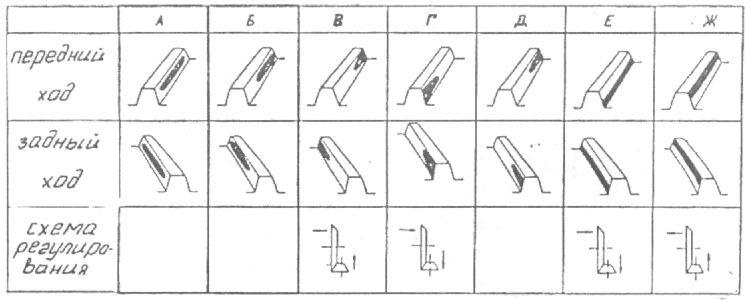
Рис. 480 Зацепление (контактные пятна) главной передачи
В ведущую шестерню 5 (Рис. 464) установить внутреннее кольцо конического роликоподшипника 24 (большего диаметра), надеть распорную втулку 4 с регулирующими прокладками 19 ... 23. Ведущую шестерню вместе с установленными на ней деталями ввести в стакан подшипков 6 в котором предварительно установлены наружные кольца подшипников 16 и 24. Затем установить на всю глубину внутреннее кольцо второго подшипника 16.
На стакане подшипников 6 поставить крышку 12 с манжетой 13. Между стаканом подшипников 6 и крышкой уплотнителя 12 вставить уплотнительную прокладку 9 и контактирующие поверхности смазать герметической смазкой. Болты 11 затянуть соответствующим моментом.
На шлицы ведущей шестерни надеть фланец 15 и затянуть гайку 14,соответствующим моментом. Проворачиванием фланца установить равномерность и соразмерность сопротивления подшипников. Гайку законтрить шплинтом 18.
В левую чашку дифференциала 34 (Рис. 481) ввести левую шестерню полуоси 49 вместе с опорной шайбой 41 или 42 (канал для смазки должен находиться со стороны шестерни). Надеть сателлиты 38 на оси 48 и ввести их в левую половину чашки дифференциала.
К чашке дифференциала закрепить магнитную стойку (Рис. 481) замерить аксиальный зазор. После вычета толщины опорной шайб сателлитного зубчатого колеса из замеренного значения, правильная величина аксиального зазора должна быть в интервале 0.6.. .0.9 мм.
Этот замер не следует проводить при помощи монтажных прокладок, так как их прогиб приводит к меньшему значению, что может привести к замеру неправильного значения.
Таким же образом собрать и проверить аксиальный зазор в правой чашке дифференциала 39. В этой чашке устанавливается и правая шестерня полуоси 40, которая приспособлена для блокировки дифференциала. При установке осей сателлитных зубчатых колес не следует допускать перемены положения последних относительно уже проверенной чашки дифференциала.
С помощью четырех болтов 33 обе чашки дифференциала вместе с шестернями присоединить друг к другу. Проверить аксиальный зазор обеих шестерен полуосей. Эта проверка производится с помощью магнитной стойки с индикатором и дорна Т19 - 1039. Аксиальный зазор должен быть в интервале 0.30...0.45 мм (Рис. 482).
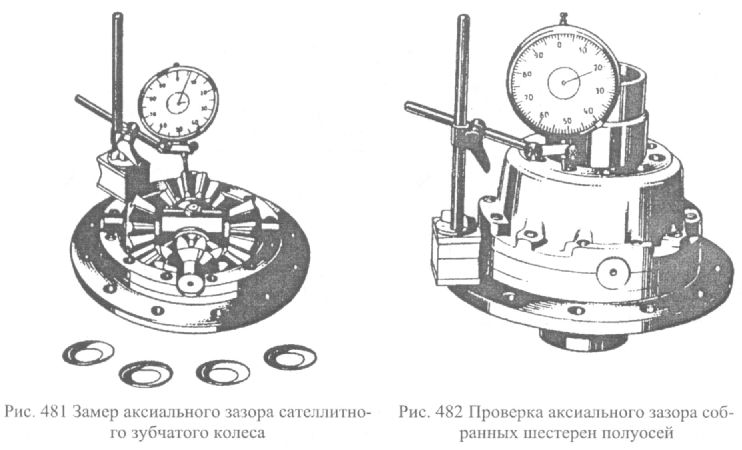
Проверенный дифференциал в сборе разобрать (перестановка деталей недопустима), смазать фрикционные поверхности и зубчатые колеса маслом, затем снова собрать. Обе половинки соединяются 12-ю болтами 33, которые затягиваются динамометрическим ключом и контрятся проволокой.
Ведомую шестерню главной передачи 35 подсоединить к коробке дифференциала с помощью болтов 52, которые затянуть соответсвующим моментом. Болты законтрить проволокой против отворачивания. Внутренние кольца подшипников 44 нагреваются до температуры не более 80° С, затем надеваются с обеих сторон на чашки дифференциала.
Картер главной передачи 32 установить на стойку для сборки Т17 - 377. Снять крышки подшипников картера 54, ввести собранный дифференциал вместе с собранными коническими роликоподшипниками в картер. К наружным концам резьбы крышки подшипников картера завернуть опорные кольца подшипников 31. Дифференциал вести с некоторым смещением относительно осевой линии ведущей шестерни, в сторону от зацепления. Не допускать перемену мест крышек подшипников. С помощью ключа Т17 - 393 завернуть до конца опорные кольца подшипников (Рис. 473).
На картере главной передачи установить регулирующие прокладки 25... 28 (Рис. 464) общей толщиной согласно расчетам в пункте 2. Далее установить стакан подшипников 6 и присоединить оба узла друг к другу болтами 2, затянуты предписанным крутящим моментом. Перед сборкой смазать уплотнительные поверхности герметической смазкой.
На балке моста замерить значения диаметра ф 340Н8 (+0089) (рис. 483). С помощью микрометра на картере главной передачи замерить размер 340m7 (+0.021+0.078) (рис 484). Путем дополнительного затягивания опорных колец подшипников, замеряемый диаметр доводится до значения действительного диаметра замеренного на балке моста, завышенного на 0.05...0.10 мм. Это завышение обеспечивает необходимый натяг конических роликоподшипников дифференциала при сборке крышки подшипников.

Перед каждым проворачиванием опорных колец подшипников, необходимо немного ослабить болты крышек подшипников, провернуть опорные кольца насколько это необходимо, затем после постукивания затянуть их болтами предписанным крутящим моментом.
С помощью индикатора и магнитной стойки замерить зазор в паре конических зубчатых колес (Рис. 475). Правильное значение зазора в интервале 0.28...0.35 мм регулируется путем равномерного ослабления опорного кольца одной из сторон и затягивания другой в зависимости от необходимости увеличить или уменьшить зазор. Замер произвести в нескольких местах. После достижения правильного зазора следует проверить и, если необходимо , скорректировать натяг. После затягивания болтов предписанным крутящим моментом, законтрить их проволокой.
Контактирующие поверхности фланца балки заднего моста и картера главной передачи смазать герметической смазкой. Собранный картер установить на контактирующую поверхность балки моста, контролируя при этом правильность монтажа. Картер закрепить болтами 45 (Рис. 465) предписанным крутящим моментом.
ВНИМАНИЕ! Картер главной передачи необходимо установить так, чтобы риска, высеченная при сборке на картере, совпадала с риской на балке заднего моста. Если балка моста или картер были заменены, необходимо еще до сборки определить их взаимное положение с помощью дорна и пометить это положение рисками.
В балке заднего моста поставить направляющие шайбы 152 (Рис. 466), установить рукав 147, с введенными в нее двумя болтами 77, до упора в опорный диаметр, затем надеть комплект суппорта колесных тормозов, после чего укрепить весь узел болтами 77, путем притягивания ключом до предписанного крутящего момента. При этой операции нужно следить за положением отверстия разжимного кулака. Пружинные шайбы 79 устанавливаются под головки болтов, за исключением болтов возле подшипников разжимных кулаков, где пружинные шайбы находятся под гайками.
С помощью дорна Т17 - 1453 в комплекте суппорта тормозных колодок установить игольчатые подшипники 146. Перед этим смазать иглы подшипников консистентной смазкой Литол - 24, чтобы они могли держаться в кольцах подшипников.
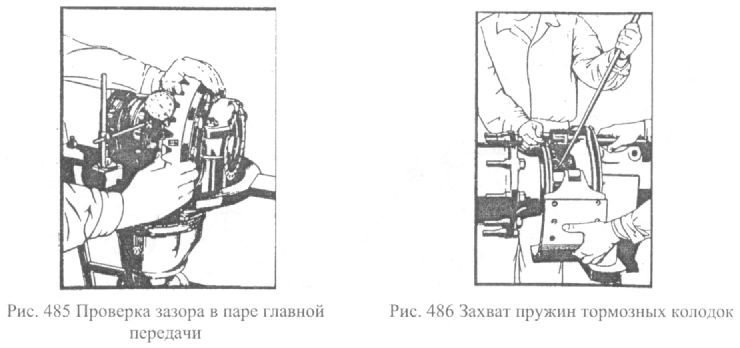
С обеих сторон подшипников установить в суппорте колесных тормозов уплотнитель 145 и шайбу 144 и «О» - кольцо. Пространство между острыми кромками уплотнителя заполнить консистентной смазкой Литол - 24.
Ввести правый и левый разжимные кулаки 156 и 157 (Рис. 467), надеть опорные кольца 150 (Рис. 466) и стопорные кольца 151. Стопорение разжимных кулаков сделать после монтажа автоматические регулировочные рычаги.
В подшипник 157 (Рис. 467) ввести втулку 160 затем «О» - кольца 161, с обеих сторон поставить закрывающие крышки 159 с помощью дорна Т17-1457 и застопорить их кольцами 158. Детали смазать консистентной смазкой Литол - 24.
Надеть собранные подшипники на разжимных кулаках и с помощью быстросъемных шайб 174... 176 установить их так, чтобы кулак проворачивался без усилии.
Размеры быстросъемных шайб следующие:
производственный № шайбытолщина, мм
332-00.00.10 0.2
332-00.00.11 0.5
332-00.00.121.0
Подшипники вместе с быстросъемными шайбами укрепляются болтами 153 и 154 затянутых предписанным крутящим моментом. Проверить свободно ли проворачиваются разжимные кулаки. В случае затрудненного проворачивания следует заново отрегулировать зазор с помощью регулирующих шайб 174... 176.
На разжимной кулак тормоза надеть уплотнитель 166 или 167, автоматические регулировочные рычаги, прокладка 169 и застопорить детали болтами 168. (Не допускать перестановки левого и правого рычага).
В суппортах колесных тормозов 83 (Рис. 466) собрать комплект тормозных колодок, установить соединительную планку 87 и законтрить стопорными шайбами 88. Приблизить тормозные колодки к эвольвенте разжимных кулаков и с помощью рычага Т17 - 411 поставить пружины 141 тормозных колодок (Рис. 486).
С помощью болтов 80 к собранному суппорту колесных тормозов закрепить предохранительные щиты 148 (Рис. 466).
В ступицу колеса 105 установить наружные кольца конических роликоподшипников 100, добиваясь их равномерного прилегания. Не допускать перестановки колец подшипников. Для этого следует пометить внутренние и наружные кольца подшипников одинаковыми цифрами.
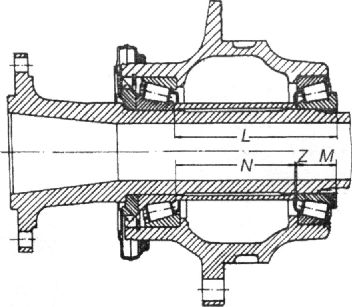
Рис. 487 Размеры для расчета сборки ступицы
Чтобы достичь при сборке конических роликоподшипников и ступицы колеса требуемого значения натяга в интервале ±0.05 мм, необходимо рассчитать толщину регулирующих прокладок 132... 135 между распорной втулкой 106 и внутренним кольцом конического роли-коподшипка. Толщина прокладок получается из соотношения (Рис. 487):
L = M + N + Z- (±0.05 ),
из которого для Z получается:
Z=L-M-N+( ±0.05 ), где
L - общее расстояние между задними опорными поверхностями внутренних колец конических роликоподшипников;
М - ширина внутреннего кольца конического роликоподшипника;
N - длина распорной втулки;
Z - толщина регулирующих прокладок.
Размеры регулирующих прокладок следующие:
производственный № прокладки толщина, мм
325-00.00.07 0,15
41-096-5101 0.3
41-097-51010.5
41 -098-5101 1.0
Ориентировочные размеры L, М и N следующие:
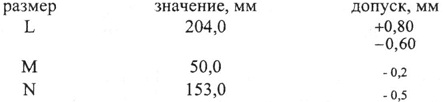
В ступицу колеса 105 установить болты 137.
В собранную ступицу установить уплотнитель 140.
На рукаве моста 147 надеть уплотнительное «О» - кольцо 139 и комплект маслособирательного кольца 97 и 98.
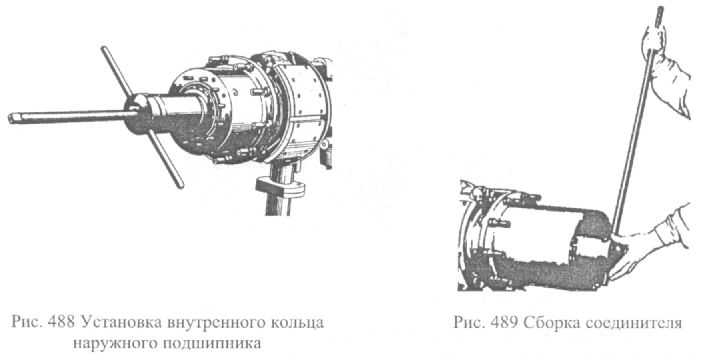
На конец рукава моста навернуть приспособление для монтажа ступицы Т17-1567. Запрессовать внутреннее кольцо первого подшипника 100, затем ввести распорную втулку 106 и регулирующие прокладки 132... 135. Собранную ступицу (вместе с наружными кольцами подшипников) ввести во внутреннее кольцо подшипника и равномерно установить внутреннее колыю второго (наружного) подшипника (Рис. 488).
К ступице колеса 105 надеть уплотнительное «О» - кольцо 104, установить картер колесного редуктора 107 и затянуть четыре винта 102.
Следом за внутренним кольцом конического роликоподшипника надеть на шлицы соединитель 108, легким постукиванием продвинуть его до упора в подшипник и укрепить гайкой с прорезями 109 с помощью ключа Т17 - 402 сответствующим моментом (Рис. 489). Проверить прокручивание собранной ступицы. В гайку с прорезями завернуть стопорящий винт 110 так, чтобы его конец попал в шлицы соединителя (для этого необходимо, чтобы гайка была завернута в подходящем положении). Таким образом гайка законтрена.
С помощью болтов 80 к собранному суппорту колесных тормозов закрепить предохранительные щиты 148 (Рис. 466).
Опорное колесо 111 установить в колесный редуктор, так чтобы его шлицы зацепились со шлицами соединителя 108.
В сателлитные шестерни 114 вставить распорные втулки 112, предварительно смазанные консистентной смазкой Литол-24 и с обеих сторон игольчатых роликов 113 и опорных шайб 115. Сателлитные шестерни последовательно вводятся в держатель, а затем и оси 119, которые следует запрессовать.
На подготовленный таким образом держатель сателлитных колес надевается «О» -кольцо 116 и весь комплект вводится в картер колесного редуктора. Необходимо следить за целостностью резинового «О» - кольца.
После правильной сборки затянуть болты 117. Болтов обезпечить клеение.
Полуось с собранными стопорными кольцами 122 и спиралями 130 и 131 ввести в шлицы полуосевых шестерен и продвинуть до осей сателлитных шестерен дифференциала. На свободные концы полуосей надеть ведущую шестерню колесного редуктора 121 и застопорить вторым стопорным кольцом 122. Замерить расстояние от торца полуоси до контактной поверхности комплекта крышки держателя сателлитных колес (расстояние А, Рис. 490), вычесть 0,5... 1,0 мм и на такую длину корректировать размер опоры полуоси, гарантирующей требуемый аксиальный зазор полуоси.
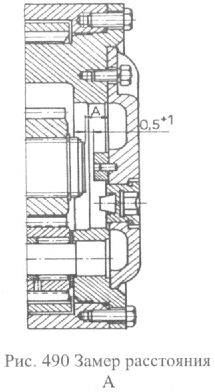
Контактирующие поверхности крышки и комплект держателя сателлитных зубчатых колес смазать герметической смазкой, установить крышку 120 и закрепить болтами 127.
Подготовленные тормозные цилиндры установить на кронштейны 162 и 163 (Рис. 467) и закрепить. Установить тормозные барабаны 101 (Рис. 466) на болты 137 и закрепить их болтами 103 к ступицам картеров колесных редукторов.
Вместе с уплотнительными кольцами 59 в балку моста завернуть заливные 58 и сливные 60 пробки. Уплотнительное кольцо 124 вместе с заливной пробкой 123 завернуть в крышку 120 колесного редуктора.
Смазать втулки разжимных кулаков, оси тормозных колодок и червячного механизма тормозных рычагов. Заправить задний мост маслом. Места смазки и контроль указаны на Рис. 491.
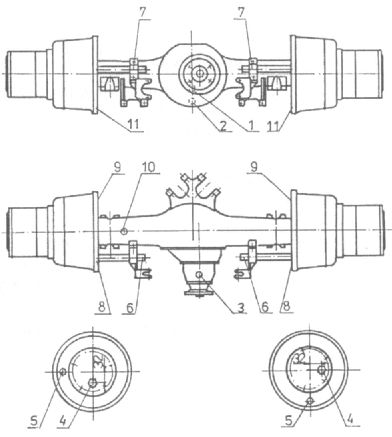
Рис. 491 Места пробки и пресс-масленки
1.Картер главной передачи
поз. 1 - маслозаливная и контрольная пробка
поз.2 - сливная пробка
поз.З - маслозаливная пробка в стакане подшипников ведущей конической шестерни
2.Колесные редукторы
поз.4 - маслозаливная и контрольная пробка
поз.5 - сливная пробка (отмеченный болт)
3.Места для смазки с конссистентными смазками
поз. 6 - пресс-масленки червячных механизмов тормозных рычагов
поз. 7 - пресс-масленки втулок разжимных кулаков в кронштейнах тормозных камер
поз. 8 - пресс-масленки втулок разжимных кулаков в суппортах тормозных колодок
поз. 9 - пресс-масленки осей тормозных колодок
4.Другие
поз. 10 - сапун
поз. 11 - масловыпускательные трубки
Периодичность смазывания маслом и консистентными смазками и необходимые количества указана в Таблица 76.
Таблица 76 Периодичность смазывания
Место смазки | Количество, (л) | Выполняемая операция | |
Проверка уровня | Смена масла | ||
Картер главной передачи | 7,5 | Через каждые 7500 кмпробега | Первая смена после 7500 кмпробега. Следугощие через каждых 30000 кмпробега |
Колесные редукторы | 2,5+2,5 | ||
Стакан конической шестерни | 0,250 | Только при первоначальномпрокручиванием | |
Втулки и подшипники разжимных кулаков, пальцытормозных колодок, червячный механизм тормозных рычагов | До необходимого количества | Через каждые 7500 кмпробега |
Замечание. Если в течение одного года мост имел пробег меньше, чем 30000 км, смену масла надо осуществить в рамках одногодичнего периода.
Таблица 77 Рекомендуемые смазочныматериалы
Трансмиссионныемасла | Консистентныесмазки |
ТМ-5/90 БДС 14368 -82 ТАп-15В ГОСТ 23652 - 79 ТСп-15К ГОСТ 23652 -79 OA-РР 90CSN или другие с качество по API-GL-5 и вискозитетномклассе по SAE 90 | АФС З об В1/Н001-Н111/РС01БДС 1415-84 Литол 24ГОСТ 21150-75 AV-2 или NH-2 CSN Замечание. 1.Не допускается смешивание различных сортовмасел ввиду различных присадок в их составе. 2.Рекомендуемые масла и консистентные смазкипригодны, когда задние мосты эксплуатируются в нормальных дорожныхусловиях и в умеренном климатичном поясе. |
После сборки ведущий мост обкатать на стенде без нагрузки.
Режим обкатки следующий:
направление вращения частота вращения(об./мин) время обкатки(мин)
передний ход25 2
140020
задний ход14005
Во время обкатки проверить плавность и шумность работы моста, герметичность моста, действие дифференциала и тормозных механизмов.
В конце обкатки последовательно затормозить левый и правый тормозной барабан и проверить действие дифференциала.
При проверке контролировать температуру (нагрев). Если в конце обкатки температура масла повысилась более 85 °С, разобрать мост и установить причину перегрева.
После обкатки слить масло из моста.
При контроле уровня шума мостов должны соблюдаться следующие условия:
-уровень шума внешнего фона не более чем 70.. .71 дБ (А);
-около стенда испытаний не должно быть больших шумоотражающих поверхностей;
-(стены, метальные панели и др.) на расстоянии менее чем пять метров;
-конструкция стенда не должна создавать условия для вибрирования и резонанса;
-контроль осуществляется на расстоянии 50 мм от Соответствующей поверхности моста.
Проверка производится с помощью калиброванного шумомера «БРЮЛ И КЕР» типа 2203 или другого подобного типа.
При этих условиях допустимый уровень шума следующий:
-93 дБ (А) для главной передачи. Замер по оси моста с задней стороны.
-91 дБ (А) для колесных редукторов. Замер по оси их крышки.
При наличии шума или стуков мост разобрать. Проверить регулировку подшипников, положение пятна контакта зубчатой пары главной передачи и при необходимости повторить соответствующую регулировку.