Рулевое управление. Часть 2
РЕМОНТ
Приступая к ремонту рулевого механизма, насоса рулевого гидроусилителя и других сборочных единиц рулевого управления, следует иметь в виду, что восстановление деталей, исчерпавших свою работоспособность вследствие износа, в этих узлах недопустимо. Изготовление таких деталей с высокой точностью и чистотой рабочих поверхностей, а также их селективный подбор при сборке возможны только в условиях специализированного производства. Ремонт рулевых механизмов и насосов в условиях автотранспортных предприятий возможен только способом замены вышедших из строя агрегатов или деталей на исправные.
Проверку и регулировку рулевого механизма на автомобиле Камаз 4308 нужно проводить при отсоединенной продольной рулевой тяге и неработающем двигателе.
Предварительно надо проверить балансировку колес, давление воздуха в шинах, наличие смазочного материала в рулевом управлении и ступицах колес, регулировку подшипников ступиц колес и рулевых тяг, работу амортизаторов, установку передних колес. Кроме того, проверить уровень масла в бачке насоса гидроусилителя, убедиться в отсутствии воздуха в системе, осадка или грязи в бачке и на фильтре насоса, утечки масла в соединениях маслопроводов.
Усилие на рулевом колесе следует измерять пружинным динамометром, прикрепленным к ободу колеса в таких его положениях:
1. Рулевое колесо повернуто более чем на два оборота от среднего положения. Усилие на рулевом колесе должно быть 5,9-15,7 Н (0,6-1,6 кгс). В этом случае зацепление и шариковинтовая пара выведены в положение, близкое к крайнему, где трение в этих узлах практически исключено, а величина усилия определяется преимущественно моментом трения в упорных подшипниках, уплотнениях и втулках рулевого механизма.
Несоответствие усилия на ободе рулевого колеса указанной величине свидетельствует о неправильной (недостаточной или чрезмерной) затяжке упорных подшипников винта, либо означает, что повреждены детали узла шариковой гайки.
Недостаточная затяжка упорных подшипников приводит к нарушению курсовой устойчивости автомобиля Камаз 4308 (автомобиль плохо держит дорогу); чрезмерная, наряду с повреждением детали узла шариковой гайки, - к заклиниванию рулевого механизма (явление остаточного давления).
2. Рулевое колесо повернуто на 3/4 оборота от среднего положения. Усилие не должно превышать 19,6-22,6 Н (2,0-2,3 кгс).
При этом положении добавляется трение в шариковинтовой паре за счет предварительного натяга шариков. Отклонение величины усилия на ободе рулевого колеса от указанных значений вызывается повреждением деталей узла шариковинтовой пары.
3. Рулевое колесо проходит среднее положение. Усилие на рулевом колесе должно быть на 3,9-5,9 Н (0,4-0,6 кгс) больше усилия, полученного при замере во втором положении, но не превышать 27,8 Н (2,8 кгс).
В этом случае проверяется регулировка зубчатого зацепления рулевого механизма. Если усилие меньше указанной величины, зазор в зубчатом зацеплении больше допустимого, автомобиль Камаз 4308 при этом будет плохо держать дорогу. Если усилие больше - зацепление слишком затянуто, что может являться, наряду с другими факторами, причиной плохого самовоз-врата управляемых колес в среднее положение.
Если при измерении усилий в перечисленных выше положениях окажется, что они не соответствуют указанным величинам, нужно отрегулировать рулевой механизм. При необходимости снять механизм с автомобиля для выполнения работ по его частичной или полной разборке и дополнительной проверке.
Регулировку рулевого механизма необходимо начинать с замера усилия в третьем положении. При этом с помощью регулировочного винта вала сошки надо довести усилие до нормы. При вращении винта по ходу часовой стрелки усилие будет увеличиваться, при вращении против хода часовой стрелки уменьшаться.
Для регулировки усилия в первом положении следует произвести частичную разборку рулевого механизма, для того чтобы подтянуть или ослабить гайку крепления упорных подшипников.
Для устранения причин несоответствия усилия во втором положении требуется полная разборка рулевого механизма. Полную разборку разрешается производить только на предприятии, ремонтирующем рулевые механизмы, или в специализированных мастерских. Порядок снятия, разборки и сборки рулевого механизма, а также его после дующей проверки и установки на автомобиль Камаз 4308 изложен ниже.
При проверке давления в гидросистеме рулевого управления на автомобиль в напорной магистрали между насосом и рулевым механизмом нужно установить приспособление (рис. 5-10), имеющее манометр 2 со шкалой до 9810 кПа (100 кгс/см2) и вентиль 1, прекращающий подачу масла к гидроусилителю.
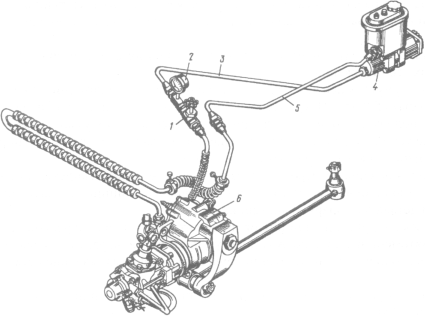
Рис. 5-10. Схема проверки давления в гидросистеме рулевого управления:1 - вентиль; 2 - манометр; 3 - магистраль высокого давления; 4 - насос; 5 - магистраль низкого давления; 6 - механизм рулевой.
При проверке давления надо открыть вентиль и повернуть рулевое колесо до упора, приложив к рулевому колесу усилие не менее 98,1 Н (10 кгс). Давление масла при частоте вращения коленчатого вала 600 мин-1 должно быть не ниже 7355 кП (75 кгс/см2).
Если давление масла будет ниже 7355 кПа (75 кгс/см2), то медленно завернуть вентиль, следя за повышением давления по манометру. При исправном насосе давление должно повышаться и быть не ниже 8335 кПа (85 кгс/см2). В этом случае неисправность нужно искать в рулевом механизме (неправильная регулировка предохранительного клапана или чрезмерные внутренние утечки). Если давление не повышается, то неисправен насос. Если давление при закрытом вентиле выше давления, которое было при открытом вентиле, но ниже 7355 кПа (75 кгс/см2), то неисправными могут быть оба агрегата.
Для проверки правильности работы клапана управления гидроусилителем нужно отсоединить продольную рулевую тягу, открыть вентиль и повернуть рулевое колесо до упора с усилием не менее 98,1 Н (10 кгс) при частоте вращения коленчатого вала 1000 мин-1.
При прекращении действия усилия на рулевое колесо давление должно понизиться до давления не выше 294-490 кПа (3-5 кгс/см2). Такую проверку необходимо провести в двух, крайних положениях. Если давление не понизится, то это свидетельствует о заедании золотника или реактивных плунжеров клапана.
При проверке нельзя держать вентиль закрытым, а колеса повернутыми до упора более 15 с. Проверку следует проводить при температуре масла в бачке плюс 65-75 °С.
В случае необходимости масло можно нагреть, поворачивая колесо до упора в обе стороны и удерживая их в крайних положениях не более 15 с.
Регулировку затяжки подшипников вала рулевой колонки надо проводить, если ощущается осевое перемещение вала, а момент вращения вала менее 29,4-78,5 Н.см (3-8 кгс.см) (что соответствует усилию 1,15-3,08 Н (0,118-0,314 кгс), приложенному на радиусе рулевого колеса 255 мм) при отсоединенном карданном вале.
Регулировать затяжку подшипников необходимо вращением регулировочной гайки, предварительно разогнув ус стопорной шайбы. При регулировке, подтягивая гайку, надо поворачивать вал за рулевое колесо в обе стороны, чтобы не перезатянуть гайку.
Недопустима затяжка гайки с последующим отворачиванием ее для получения указанного момента вращения вала рулевой колонки, так как при этом могут быть повреждены штампованные из листовой стали кольца подшипников вала рулевой колонки. После окончания регулировки один из усиков стопорной шайбы вновь загнуть в паз гайки. Если по каким-либо причинам колонка рулевого управления разбиралась, то при сборке в подшипники вала заложить свежий смазочный материал.
При сборке карданного вала нужно следить за тем, чтобы оси отверстий в вилках для крепежных клиньев находились в параллельных плоскостях и были расположены так, как это показано на рис. 5-2. Карданный вал следует устанавливать на автомобиль Камаз 4308 таким образом, чтобы вилка со шлицевой втулкой была обращена вверх. При этом заложенный в полость втулки смазочный материал обеспечивает лучшее смазывание шлицев.
Замену поперечной рулевой тяги рекомендуется выполнять в следующем порядке:
- вывесить переднюю ось автомобиля;
- расшплинтовать и отвернуть гайку, соединяющую шаровой палец левого наконечника тяги с соответствующим нижним рычагом поворотного кулака;
- выбив шаровой палец из конусного отверстия рычага, отсоединить левый наконечник тяги рулевой трапеции;
- проделать те же операции с правым наконечником поперечной рулевой тяги и снять тягу с автомобиля;
- установить концы шаровых пальцев наконечников новой поперечной тяги в отверстиях нижних рычагов, затянуть и зашплинтовать гайки крепления. Момент затяжки гаек крепления шаровых пальцев поперечной рулевой тяги 245-315 Н.м (25-32 кгс.м). Установку поперечной тяги производить так, чтобы масленки шаровых пальцев на наконечниках тяги были обращены назад по ходу автомобиля;
- опустить переднюю ось.
Для замены продольной рулевой тяги:
- вывесить переднюю ось автомобиля и повернуть управляемые колеса влево до отказа;
- расшплинтовать и отвернуть гайку крепления шарового пальца продольной рулевой тяги со стороны сошки рулевого управления;
- выбив шаровой палец из конусного отверстия сошки, отсоединить тягу;
- выполнить те же операции с другим шарнирным соединением продольной тяги в месте соединения ее с верхним рычагом левого поворотного кулака и снять тягу с автомобиля.
Установку новой продольной тяги нужно производить в последовательности, обратной снятию, обратив при этом внимание на правильность присоединения и соответствие отличающихся головок тяги местам установки. Опустить передний мост автомобиля. Гайки крепления шаровых пальцев продольной рулевой тяги затянуть с моментом 245-314 Н.м (25-32 кгс.м).
Для снятия рулевого колеса, если оно не снимается от легких постукиваний молотком снизу вверх, следует использовать съемник. Предварительно сняв декоративную крышку и отвернув гайку крепления рулевого колеса, ввести крюки захвата 2 (рис. 5-11) в отверстие ступицы рулевого колеса и повернуть по ходу часовой стрелки до упора. Упирая наконечник 3 в торец вала, вворачивать винт 1 в захват до полного снятия рулевого колеса.
При установке рулевого колеса затянуть гайку крепления его, обеспечив момент затяжки 59-79 Н.м (6-8 кгс.м).
Для проверки, регулировки и ремонта предохранительного клапана рулевого механизма при отказе или нестабильной работе нужно:
- слить масло из системы рулевого гидроусилителя;
- сняв пломбу и расшплинтовав пробку гнезда предохранительного клапана, промыть ветошью, смоченной керосином или дизельным топливом, бобышку корпуса клапана управления гидроусилителя, в которой размещен предохранительный клапан;
- отвернуть пробку гнезда предохранительного клапана и, вынув неисправный клапан, закрыть отверстие в корпусе клапана гидроусилителя чистой бумагой или салфеткой;
- промыть клапан керосином и проверить отсутствие забоин и посторонних частиц на его корпусе, посадочных кромках игольчатого клапана, на седле и на внутренних поверхностях отверстия в корпусе клапана управления. Посторонние частицы осторожно удалить. Проверить также целостность резинового уплотнительного кольца и пружин клапана;
- если внешним осмотром клапана неисправность выявить не удается, проверить предохранительный клапан (эту проверку можно выполнять только в специализированных мастерских, приспособленных для работ с гидроаппаратурой) в специальном приспособлении, позволяющем подвести масло под давлением к входному отверстию предохранительного клапана, таком, как, например, нагрузочно-измерительный стенд МТ-60 производства STOLECZNE ZAKLADY BYDOWY MAS-ZYNIKI (Польша).
При давлении масла до 6377 кПа (65 кгс/см ) утечки из-под предохранительного клапана недопустимы.
Если утечки имеют место, клапан надо осторожно разобрать и продуть детали струей сжатого воздуха. Клапан должен открываться полностью при давлении 7357,5-7848,0 кПа (75-80 кгс/см2).
При отсутствии специального приспособления допускается проверку регулировки предохранительного клапана проводить на автомобиле.
Клапан следует отрегулировать вращением резьбовой пробки. После регулировки резьбовую пробку необходимо законтрить. Зашплинтовать контргайку проволокой и поставить пломбу.
Для облегчения сборки и во избежание защемления уплотнительного кольца рекомендуется посадочное место в отверстии корпуса клапана управления и само кольцо смазать смазкой ПВК ГОСТ 19537-74;
- промыть и заправить систему.

Рис. 5-11. Съемник рулевого колеса: 1 - винт; 2 - захват; 3 - наконечник.
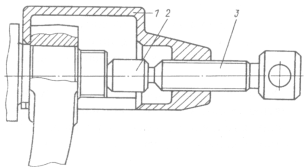
Рис. 5-12. Съемник сошки руля: 1 - захват; 2 - наконечник; 3 - винт.
Для снятия рулевого механизма нужно:
- поднять кабину в первое положение (41°);
- отогнув усики упорной шайбы, отвернуть гайку крепления верхней головки сошки 9(рис. 164);
- съемником снять сошку, вворачивая винт 3 (рис. 5-12) в захват 1 съемника и упираясь наконечником 2 в торец вала сошки (выколачивание сошки может вызвать поломку деталей);
- вывернуть магнитную пробку и слить масло из картера рулевого механизма, для более полного слива повернуть рулевое колесо 2-3 раза из одного крайнего положения в другое;
- отсоединить трубопроводы высокого и низкого давления от руле вого механизма и слить оставшееся в насосе масло;
- отсоединить карданный вал рулевого управления от рулевого механизма, для этого вынуть шплинт, отвернуть гайку клина и выбить клин;
- вывернуть болты крепления картера рулевого механизма к кронштейну передней рессоры и снять рулевой механизм;
- тщательно очистить и промыть наружную поверхность рулевого механизма;
- слить остатки масла, перевернув рулевой механизм клапаном вниз и поворачивая вал ведущего зубчатого колеса рулевой передачи 2-3 раза из одного крайнего положения в другое.
При установке рулевого механизма на автомобиль Камаз 4308 необходимо:
- установить механизм на передний кронштейн левой передней рессоры и закрепить его болтами с моментом затяжки 275-314 Н.м (28-32 кгс.м);
- подсоединить нагнетательный и сливной трубопроводы к клапану управления гидроусилителем;
- присоединить карданный вал рулевого управления к рулевому механизму, предварительно совместив отверстие в вилке кардана и лыску под клин на вале ведущего зубчатого колеса, забить клин, завернуть и зашплинтовать гайку с моментом затяжки гайки крепления клина 13,7-16,7 Н.м (1,4-1,7 кгс.м);
- залить масло и прокачать систему гидроусилителя;
- надеть сошку рулевого управления на вал рулевого механизма, установить шайбу, навернуть гайку, затянуть ее с моментом 490-550 Н.м (50-56 кгс.м) и застопорить шайбой;
- проверить герметичность соединений и шлангов гидросистемы рулевого управления. Подтекание масла из соединений не допускается.
Разборку и проверку рулевого механизма надо проводить в следующем порядке:
1. Вывернув болты крепления, снять боковую крышку вместе с валом сошки. При извлечении вала сошки предварительно очистить его шлицованный конец.
2. Проверить осевое перемещение регулировочного винта в вале сошки. Если перемещение превышает 0,15 мм, отрегулировать осевой зазор путем подбора регулировочной шайбы. Регулировочный винт должен иметь осевое перемещение относительно вала сошки 0,02-0,08 мм и вращаться при этом плавно, без заеданий. Стопорное кольцо должно полностью входить в канавку вала сошки.
Это необходимо для надежного соединения деталей данного узла. При необходимости следует заменить уплотнительное кольцо регулировочного винта, применяя оправку. После сборки с боковой крыш кой вал сошки должен свободно проворачиваться от усилия руки, а регулировочный винт оставаться неподвижным (проверять без контр гайки).
3. Вывернуть болты крепления, снять переднюю крышку. При всех последующих операциях разборки и сборки необходимо помнить, что выворачивание винта рулевого механизма из шариковой гайки более чем на два оборота от среднего положения может привести к выпада нию шариков и заклиниванию винта.
4. Отвернуть гайки крепления корпуса клапана управления гидроусилителем и осторожно выдвинуть корпус вперед настолько, чтобы его можно было провернуть относительно винта, не касаясь шпилек корпуса рулевой передачи.
5. Проверить затяжку гайки упорных подшипников и плавность вращения корпуса клапана управления относительно винта. Момент, необходимый для проворачивания корпуса клапана управления, должен быть равен 98,1-122,6 Н.см (10-12,5 кгс.см) (в ходе эксплуатации допускается падение момента вращения до 34,3 Н.см (3,5 кгс.см).
В случае несоответствия момента указанной величине отрегулировать затяжку гайки упорных подшипников.
Если вращение корпуса клапана неплавное (сопротивление вращению переменно), заменить подшипники. Для регулировки затяжки или замены подшипников необходимо отжать буртик гайки, вдавленный в паз винта, и отвернуть гайку, удерживая от проворачивания ведущее зубчатое колесо рулевой передачи.
Предупреждение. При отворачивании гайки упорных подшипников необходимо обязательно удерживать первичный вал рулевой передачи от проворачивания. Несоблюдение этого правила ведет к поломке усика пружинной шайбы 23 (рис. 5-4) и порче резьбы винта 17.
При снятии корпуса клапана управления следить, чтобы золотник и реактивные плунжеры не выпадали, так как при заводской сборке каждый из них индивидуально подобран к своему отверстию.
Нельзя допускать смешивания колец упорных подшипников, следует сохранить их комплектность.
6. Проверить рукой плавность перемещений реактивных плунжеров и золотника в корпусе клапана управления гидроусилителем. Если ощущаются заедания, изменение усилия, необходимого для перемещения упомянутых деталей, поочередно вынуть заедающие детали. Устранить причину заедания, промыть и установить их на место.
7. Проверить герметичность обратного клапана, для чего залить в его отверстие масло. Утечка масла допустима только в виде отдельных капель.
8. Вывернув болты крепления и отвернув две гайки, снять рулевую передачу вместе с винтом и поршнем-рейкой.
9. Вынуть щипцами упорное кольцо 3 и осторожно снять с винта рулевую передачу.
10. Проверить, нет ли осевого перемещения шариковой гайки относительно поршня-рейки. В случае необходимости подтянуть или заменить два установочных винта и раскернить их.
11. Проверить посадку шариковой гайки на средней части винтовой канавки винта.
Гайка должна вращаться на винте без заеданий, а осевое перемещение ее относительно винта не должно превышать 0,3 мм.
Если имеет место неплавное вращение винта в шариковой гайке, при условии, что осевое перемещение не превышает 0,3 мм, заменить комплект шариков.
Для замены комплекта шариков следует предварительно выполнить следующее:
- специальным ключом с достаточно большим плечом вывернуть установочные винты шариковой гайки;
- вынуть из поршня-рейки шариковую гайку с винтом, придерживая от выпадания желобки и шарики;
- вынуть желобки, осмотреть их и, если язычки повреждены, заменить;
- затем, поворачивая винт относительно гайки в ту или другую сторону, удалить шарики и положить их в отдельную коробку.
Не допускается установка шариков, у которых разность размеров по диаметру более 0,002 мм. При несоблюдении указанного требования может произойти разрушение шариков и заклинивание рулевого механизма.
После замены шариков гайка должна проворачиваться в средней части винтовой нарезки винта под действием крутящего момента 29,4-78,5 Н.м (3-8 кгс.м), по краям посадка гайки должна быть свободной.
Дорожки качения на винте и гайке не должны иметь повреждений. Если дорожки качения повреждены (имеют вмятины, заусеницы и т. п.), заменить весь комплект винт-шариковая гайка-шарики.
12. Осмотреть рабочие поверхности цилиндра гидроусилителя. В случае отдельных задиров на зеркале цилиндра их следует удалить шабером. Отдельные продольные риски и царапины на зеркале цилиндра (без заусенцев) не являются браковочным признаком.
13. Проверить регулировку бокового зазора между зубьями колес рулевой передачи. Боковой зазор между любыми парами зубьев должен находиться в пределах 0,02 - 0,07 мм, а момент вращения ведущего зубчатого колеса в рулевой передаче не должен превышать 49,1 Н.м (5 кгс - см).
Регулировка бокового зазора в зубьях колес рулевой передачи производится перемещением узла ведущего зубчатого колеса путем подбора пакета прокладок под фланцем корпуса ведущего колеса. При этом должно быть установлено не менее трех прокладок толщи ной 0,05 мм.
При правильном зацеплении конических зубчатых колес отпечаток пятна контакта должен иметь эллиптическую форму и располагаться ближе к внутренней, узкой части зуба. Выход пятна контакта на кромки зуба недопустим.
В случае разборки рулевой передачи нельзя нарушать комплектность корпуса рулевой передачи и пары конических зубчатых колес.
Сборку механизма рулевого управления нужно производить в условиях, обеспечивающих чистоту, в порядке, обратном разборке, в соответствии со следующими указаниями:
1. Все детали разобранного механизма тщательно промыть и просушить, внутренние каналы и отверстия после промывки продуть сухим сжатым воздухом. Нельзя протирать детали ветошью, оставляющей на них нитки, ворс и т. п.
2. Все соприкасающиеся поверхности деталей рулевого механизма перед сборкой смазать маслом турбинное Тп-22 ГОСТ 9972, или маслом марки «Р».
3. Все резиновые уплотнительные детали осмотреть и заменить. Фторопластовые кольца уплотнений поршня и винта не должны иметь повреждений. Для облегчения установки резиновых колец и во избежание защемления их при сборке допускается применять смазку ПВК ГОСТ 19537.
4. В случае замены манжет вала сошки и вала ведущего зубчатого колеса рулевой передачи запрессовку их осуществлять плавно и без перекосов, применяя оправки. Окончательно указанные манжеты запрессовывать пакетом вместе с наружной манжетой и другими деталями, входящими в упомянутые узлы уплотнений, до упора в корпус механизма. При установке манжет вала сошки рабочие кромки их должны быть защищены от повреждений шлицами вала.
5. Момент затяжки болтов М8 должен быть равен 20,6-27,5 Н.м (2,1-2,8 кгс.м), болтов и гаек М10 - 34,3-41,2 Н.м (3,5-4,2 кгс.м). Упорная крышка узла ведомого зубчатого колеса передачи должна быть затянута с моментом 43,2-60,8 Н.м (4,4-6,2 кгс м) и застопорена раскерниванием ее края в паз на корпусе рулевой передачи.
Гайка крепления подшипников ведущего зубчатого колеса рулевой передачи должна быть затянута с моментом 39,2-58,9 Н.м (4-6 кгс.м) и застопорена путем вдавливания буртика гайки в паз на вале ведущего колеса.
После сборки ведомое и ведущее зубчатые колеса рулевой передачи должны свободно вращаться и не иметь ощутимого осевого зазора.
Магнитную пробку сливного отверстия (с конической резьбой и цилиндрическим магнитом) затягивать с моментом 33,4-39,2 Н.м (3-4 кгс.м).
6. Сборку шариковинтовой пары и установку собранного комплекта в поршень-рейку производить в следующем порядке:
- надеть на винт со стороны винтовой канавки плавающую уплотнительную втулку;
- установить гайку на нижнем конце винта, совместив отверстия гайки, в которые входят желобы, с винтовой канавкой винта;
- заложить 23 шарика через обращенное к рулевой передаче отверстие в гайке, поворачивая винт против хода часовой стрелки;
- заложить 8 шариков в сложенные вместе желобы и предотвратить их выпадание, замазав выходы желоба смазкой ПВК ГОСТ 19537;
- вложить желобы с шариками в гайку, поворачивая в случае необходимости винт, и обвязать гайку, чтобы предотвратить выпадание желобов;
- проверить момент вращения гайки на средней части винта (должен быть равным 29,4-78,5 Н.м (3-8 кгс.м); в случае несоответствия момента указанной величине заменить комплект шариков, не допуская перемешивания комплектов;
- запрессовать гайку с винтом в отверстие поршня-рейки, ввернув и раскернив установочные винты в двух местах против канавок в поршне-рейке. Момент затяжки установочных винтов должен быть равен 49,1-58,9 Н.м (5-6 кгс.м). В случае совпадения канавки в поршне-рейке со шлицем винта последний заменить.
Выступание винтов над цилиндрической поверхностью поршня-рейки недопустимо. Это вызовет задир рабочей поверхности цилиндра гидроусилителя.
7. При сборке рулевой передачи с винтом и плавающей уплотнительной втулкой убедиться в надежности установки упорного кольца последней в канавку упорной крышки рулевой передачи. Кольцо должно полностью входить в упомянутую канавку.
8. Устанавливать поршень-рейку в картер с помощью оправки без перекосов.
9. При сборке клапана управления гидроусилителем проследить за тем, чтобы выточка на торце золотника была обращена к рулевой передаче, а фаски на реактивных плунжерах - наружу. После сборки золотник, обратный клапан, а также реактивные плунжеры должны перемещаться в соответствующих отверстиях корпуса клапана управления плавно, без заеданий.
10. При сборке клапана управления гидроусилителем с винтом упорные подшипники необходимо устанавливать так, чтобы их большие кольца были обращены к золотнику. Пружинная шайба упорных подшипников должна быть установлена вогнутой поверхностью в сторону подшипника. После регулировки момента, необходимого для проворачивания корпуса клапана управления 98,1-122,6 Н.м (10-12,5 кгс.см), гайку крепления упорных подшипников необходимо застопорить вдавливанием буртика гайки в канавку винта рулевого механизма.
11. При сборке регулировочного винта и вала сошки обеспечить осевое перемещение винта относительно вала сошки 0,02-0,08 мм подбором регулировочной шайбы. При необходимости заменить уплотни тельное кольцо регулировочного винта, применяя оправку.
12. Отрегулировать зубчатое зацепление в паре поршень-рейка - зубчатый сектор вала сошки в соответствии с указаниями, изложенными выше. После окончания регулировки зацепления регулировочный винт сошки закернить, затянув контргайку с моментом 58.9-63,8 Н.м (6-6,5 кгс.м), удерживая при этом регулировочный винт от поворота.
После сборки рулевой механизм должен соответствовать следующим требованиям:
1. Полный угол поворота вала сошки должен быть не менее 90°.
2. После вращения винта рулевого механизма до упора поршня и приложения к ведущему зубчатому колесу дополнительного момента вращения не менее 19,6 Н.м (2 кгс.м) центрирующие пружины должны обеспечить его четкий возврат в исходное положение. Указанное условие должно соблюдаться при поворотах как вправо, так и влево.
3. Момент, прилагаемый при вращении ведущего зубчатого колеса (или усилие на ободе рулевого колеса, приложенное на радиусе 250 мм), должен быть:
- после поворота ведущего колеса более чем на два оборота в любую сторону от среднего положения 147-294 Н.см (15-30 кгс.см), (усилие на ободе рулевого колеса равно 5.9-11,8 Н (0,6-1,2 кгс);
- при повороте ведущего колеса с переходом через среднее положение при гарантированном зазоре в зубчатом зацеплении рейки-поршня и вала сошки 196-441 Н.см (20-45 кгс.см) (усилие на ободе рулевого колеса равно 7,8-17,7 Н (0,8-1,8 кгс);
- при повороте ведущего колеса с переходом через среднее положение после регулировки зубчатого зацепления рейки-поршня и вала сошки - 98,1-147,2 Н.см (10-15 кгс.см), на 3,9-5,9 Н (0,4-0.6 кгс) больше, чем при гарантированном зазоре, но не более 540 Н.см (55 кгс.см), 21,6 Н (2,2 кгс).
4. Дополнительно испытать рулевой механизм на стенде, оборудованном насосом с подачей не менее 9,0 л/мин и обеспечивающем подвод масла к отверстию корпуса клапана управления гидроусилителем. Испытание проводить на масле марки «Р» при температуре его не ниже плюс 40 °С. Перед испытанием удалить из системы воздух.
Отрегулировать предохранительный клапан стендового насоса на давление открытия 5390 кПа (55 кгс/см2) и проверить:
- вращение ведущего зубчатого колеса в любую сторону при моменте сопротивления вращению вала сошки 0 и 1275 Н.м (130 кгс.м) должно быть плавным, без заеданий;
- давление на входе в клапан управления гидроусилителя при нейтральном положении золотника должно быть не более 294 кПа (3 кгс/см2);
- момент на ведущем зубчатом колесе при сопротивлении на валу сошки 1275 н.м (130 кгс.м) - не более 1766 Н.см (180 кгс.см);
- утечку на выходе из клапана управления гидроусилителем при повороте ведущего зубчатого колеса до упора вправо или влево (время замера не более 20 с, начало замера через 5 с после поворота винта до упора) - не более 1200 см3/мин;
- поворот вала сошки из одного крайнего положения в другое должен происходить от усилия с моментом не более 118 Н.м (12 кгс.м).
Отрегулировать предохранительный клапан стендового насоса на давление открытия 90 л/мин и проверить:
- давление в нагнетательной магистрали при повороте ведущего колеса до упора вправо и влево; оно должно быть 7355-7846 кПа (75-80 кгс/см2). После снятия усилия с винта без притормаживания и остановки вала ведущего зубчатого колеса давление должно быстро падать до величины не более 294 кПа (3 кгс/см2);
- герметичность рулевого механизма в обоих крайних положениях поршня (по 5 мин в каждом положении) при давлении 8826 кПа (90 кгс/см2). Давление обеспечить установкой клапана на возвратной линии;
- правильность характеристики включения. Свободный ход на валу ведущего зубчатого колеса (угол поворота вала до повышения величины давления в напорной магистрали на 78,5 кПа (0,8 кгс/см2) должен быть 3-5° в каждую сторону. Суммарный свободный ход (сумма углов вправо и влево) допускается не более 10°.